Sigma-Aldrich has a passion for process improvement. Our aims are to look
for new and better ways to serve our customers and substantially reduce
operating costs.
Model for Improvement |
|
Process improvement, over the past five years, has become an integral part of our culture and a tremendous success story. Above all, we're looking for improved ways to serve our customers and consequently increase the demand for our Life Science and High Technology products. Furthermore, by developing more efficient processes, we can also reduce costs. This is an area where everyone in the Company worldwide can contribute to improving our performance.
Well, what is process improvement? It's a methodology for testing and
implementing changes - changes that will result in improvement. As most
of us know, from our business or private life, not all change is an improvement.
So it's important to make the right changes.
At its simplest level, “Low Hanging Fruit,” we're talking
about using common sense ways to save money that produce immediate results.
Such improvements are often a matter of doing the obvious. And no savings
is too small to be addressed. At Sigma-Aldrich, we aim to spend the Company's
money as carefully as we would our own!
In comparison, our “High Hanging Fruit” projects require
fundamental changes that produce substantial improvements. These projects
often require teamwork across business divisions and country boundaries.
In many cases the goal is often to transfer knowledge gained at one location
to another.
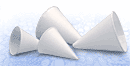 |
Sigma-Aldrich employee Louise DeMay realized the exact paper
funnel her dentist asked her to use could serve as a disposable tool
for chemical weighing. The funnels eliminate the need to clean and
dry a plastic funnel for reuse - a low hanging fruit idea that's a
real time saver. |
The model we're using to implement major change is one of "trial
and learning", the principles of which are outlined in The Improvement
Guide, co-authored by our long-time consultant and advisor Tom Nolan,
the 2000 recipient of the prestigious Deming Medal from the American Society
for Quality. First we define our aim - what we are trying to accomplish?
Next we determine measures - how will we know that a change is an improvement?
And finally we consider possible changes that will result in an improvement.
Then we test with a PDSA cycle (Plan, Do, Study, Act).
Using this approach, our initiatives have already resulted in substantial
accumulated savings of about $25 million. If we use our formula $1 saved
= $5 sales, that is equivalent to roughly sales of $125 million. These
savings have made it possible for us to make major investments in new
systems (SAP computer software and the Internet), additional R&D facilities
and researchers and an expanded sales and marketing force.
Cycle Time from Brand Locations to Subsidiaries |
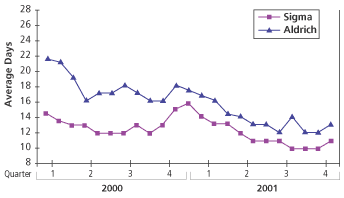 |
Cycle time refers to the time it takes to ship product from one of our brand
warehouses to a subsidiary location. After averaging 20 days in 2000, our brands dramatically decreased cycle time in 2001 by implementing a number of process improvements. Our customers appreciate the improved service. |
Initially our key improvements were in operations, but now there are PDSA's
going in almost all departments. We've launched major worldwide initiatives
in production, purchasing, packaging, labeling and distribution, all of
which will help us improve service and better manage inventory. Regarding
production, our First Pass initiative (reduce batch failures) has met
with great success. This certainly helps our profitability. We're also
using an even more sophisticated statistical approach to determine the
optimum composition of our Cell Culture products i.e. to give the best
cell growth and to design R&D projects.
Bearing in mind that we purchase over $250 million in chemicals and supplies
every year, the potential here for cost savings is enormous. And, we intend
to get them. This is in fact a very complex project for we have so many
products and purchasing in so many countries.
Packaging using "work cell" concepts coupled with better scheduling
has not only increased productivity but has substantially reduced cycle
times, resulting in the lowest levels of backorders worldwide in recent
history. This really helps research sales. Our Fine Chemicals division
has produced equally impressive packaging results. Not only were cycle
times reduced and the percentage of orders shipped on time increased,
but lead times quoted to customers were also reduced from five days to
three days. No doubt this accounts for part of the exceptional 2001 Fine
Chemicals sales growth in 2001. And, there's still plenty of room for
further improvement.
Sigma-Aldrich Worldwide Process Improvement |
|
Aim
Measures
Changes
|
The worldwide Label on Demand project will help Sigma-Aldrich improve
customer service, reduce back- orders, increase plant utilization and
control inventory because all product labels will be available wherever
Sigma-Aldrich material is located.
Major Focus Areas |
|
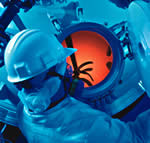 |
- Production
- Purchasing
- Packaging
- Labels
- Distribution
|
Distribution continues to be a focus for process improvement. And, in
2001, we considerably reduced distribution cycle times to our subsidiaries
and customers outside the USA. This certainly helped our international
sales which grew twice as fast as in the USA.
All these major projects will help us to reduce our level of inventory.
There were also numerous local initiatives which we expect to further
increase as we intensify our efforts.
Process improvement has already changed the way we do business at Sigma-Aldrich
and will play an even more important role in the future. Clearly, process
improvement takes out tremendous costs, improves our service and above
all helps maintain our leadership in Life Science and High Technology.
|