BUNGE'S SAFETY POLICY
• |
No work is so important or urgent that it cannot be performed safely.
|
• |
All work-related injuries, illnesses and unsafe practices are preventable.
|
• |
All personnel are responsible and accountable for their own safety and the safety of others.
|
• |
Safety performance is a key indicator of operational excellence. |
|
|
|
 |
To be the world's best agribusiness and food company, Bunge also must strive to be the safest. We reinforce our commitment to safety through continuous training, communication, benchmarking and best practice sharing. Our goal is to have no work-related injuries or illnesses and to provide our customers and consumers with products of the highest safety, quality and value.
WORKPLACE SAFETY
Bunge believes that all workplace injuries and work-related illnesses can be prevented. Our employees follow a simple rule: No work is so important or urgent that it cannot be performed safely.
Each Bunge facility around the world adheres to our Safety Policy and our Global Safety Rules, which prescribe numerous safety practices, including work habits, use
of protective equipment, machinery operation and hazardous materials handling. All facilities must meet these global safety standards along with all relevant national, regional and local regulations. Our local management teams develop site-specific rules and guidelines designed for their particular operations, plants, equipment and work environments.
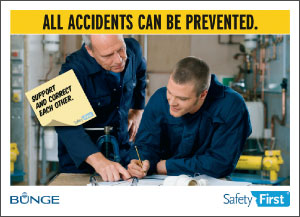
Since 2004, the Safety First campaign has helped Bunge improve safety performance in our European operations. The latest phase of the campaign emphasizes the role each employee plays in creating a zero-accident culture – making safety top of mind, reporting all potential safety issues and supporting our colleagues on the job every day.
|
 |
We evaluate our safety performance in a variety of ways. One very important measure is safety frequency – the number of lost-time accidents (those that cause employees to miss one or more days of work) per every 200,000 hours worked. Many facilities also track key safety management activities, such as levels of accident prevention, emergency preparedness, communication and training. By measuring these leading indicators,
we can assess safety performance and take corrective action – before accidents happen.
Maintaining a safe workplace requires vigilance, focus and teamwork. As a part of our ongoing safety training, employees at our plants and facilities learn that they are accountable for their own safety and that of others.
|