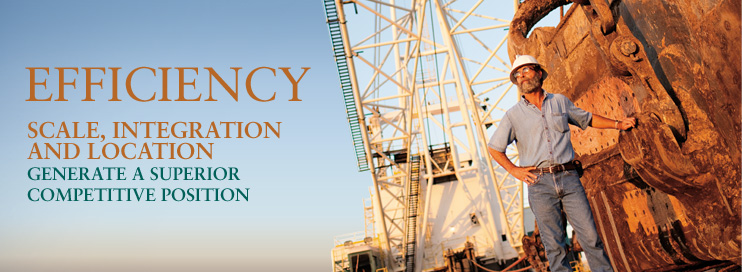
When it comes to our Phosphates business, big numbers count. Consider that Mosaic is the largest finished phosphate producer in the world. Annual capacity is 10 million tonnes — almost as large as its closest three competitors combined. Clearly, at Mosaic, phosphate is big business.
It is also a business that is meeting big demand. We forecast that global phosphate demand will increase 2.0% to 2.5% per year through 2020. That forecast, based on demand of 36 million tonnes of P205 in 2008, implies that the world must supply an additional 800,000 to one million tonnes of phosphate each year during the next decade in order to meet projected demand.
800,000 - 1,000,000 ADDITIONAL TONNES of PHOSPHATE needed each year during the next decade to meet projected demand
Mosaic's Phosphates business is well positioned to grow value and maintain its industry leadership and cost competitiveness. Vast operations that realize enormous economies of scale are among the reasons why we enjoy one of the lowest-cost positions in the global phosphate industry. Vertical integration is another. Our significant rock reserves, coupled with granulation plants and a global supply chain, provide a significant advantage over producers who must buy rock or phosphoric acid from third parties. Mosaic also produces up to one third of its needed ammonia. Sulfur is obtained through a logistics and transportation network along the Gulf Coast that enables efficient delivery of this key input.
Strategic Locations
Our competitive edge in phosphates is also firmly grounded in geography. Mines and plants are located in central Florida near Tampa Bay, which provides a deepwater port from which to ship product around the world. Florida-based operations are close to sulfur producers on the Gulf Coast. Ammonia and granulation facilities reside on the Mississippi River in Louisiana, which provides a direct route to customers in the heart of North American farming.
Complementing these strategic locations is a global distribution network that is unmatched in the industry. This network includes ports, barges, vessels, warehouses, blending and bagging facilities, as well as people.
Integrated Processed Phosphate
Fertilizer Capacity
(million tonnes product)
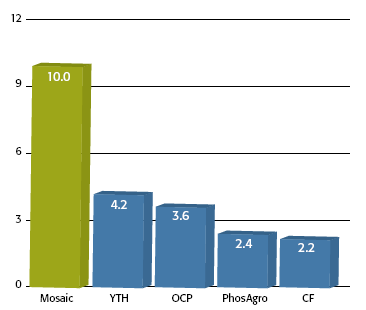
Continuous Improvement
Though scale and location provide inherent strengths, our Phosphates business relies on technology and ingenuity to ensure that Mosaic further leverages its strong asset base and maintains its competitive advantages. Investments in waste-heat recovery systems, for example, are enabling us to increasingly supply our own electrical needs.
A focus on continuous improvement is stronger than ever. Using methods such as LEAN and Six Sigma, dozens of continuous improvement teams are working at any given time to find ways to enhance efficiency and productivity. During fiscal 2009, 45 teams completed continuous improvement projects that translated into $36 million in cost and opportunity savings.
One project, for example, engaged employees to increase mined rock recovery rates. The International Quality and Productivity Center recognized this achievement with its top award for the Best Process Improvement Project completed within 90 days. On another project, a facility team identified a half-million dollars in energy savings over the course of a few months simply by improving equipment maintenance and reliability.
From extending the life of swing wires on dredge lines that improves safety and increases productivity to improving railyard flow that reduces cycle times, our Phosphates business is leaving no stone unturned in its quest to push its world-class operations to an even higher level. Beyond the cost savings and higher productivity rates, the true value in these projects lies with those who are finding solutions — engaged employees. By empowering those who are closest to day-to-day operations, we are building a culture and workforce that is as unique and competitive as its scale, location and integrated assets.
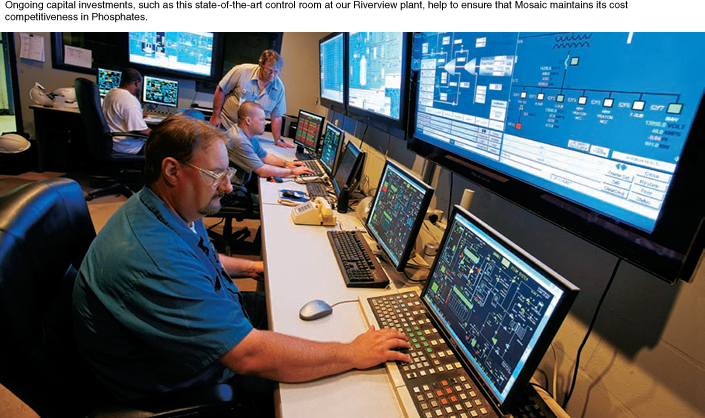